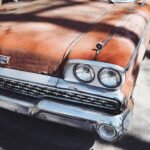
Is Selling My Car Online a Good Choice for Older SUVs and Trucks in Mobile, AL?
December 9, 2024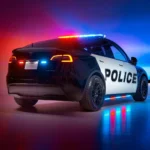
AI Technology in Police Vehicles
December 13, 2024In the world of powder coating, achieving the perfect finish isn’t just about the coating itself—it’s also about the oven that cures it. With technology advancing, many manufacturers wonder if their powder coating ovens are ready for hybrid curing techniques. Hybrid curing combines different heat sources to optimize the curing process, especially useful for complex coatings or substrates. This approach has raised interest across industries looking for faster, more versatile, and energy-efficient solutions. So, are modern powder coating ovens up for the challenge? Let’s explore how these ovens adapt to hybrid techniques and deliver superior results.
Seamless Integration of Dual Heat Sources for Versatile Curing
Today’s powder coating ovens are designed to handle more than just traditional convection heat. Many models now seamlessly integrate dual heat sources, often combining convection with infrared (IR) technology. This combination allows the oven to target specific areas of the coated object more precisely, leading to faster curing times and improved finishes. The addition of infrared heating elements within the oven chamber ensures that thicker or unevenly coated parts receive adequate heat, making the process more efficient overall.
This integration isn’t just about adding extra heat; it’s about how the different heat sources work together. By having both convection and IR heat sources within the same chamber, the oven can deliver a uniform cure, even on challenging shapes and surfaces. This versatility makes hybrid curing a practical solution, especially when switching between different types of powder coatings or materials that respond better to a specific kind of heat.
Adaptable Chamber Design to Accommodate Multiple Curing Methods
Adaptable chamber design plays a crucial role in supporting hybrid curing techniques. Powder coating ovens with adjustable interiors can accommodate varying part sizes and shapes, making it easier to apply multiple curing methods. For example, many modern ovens feature adjustable shelving or rack systems, which allow for better airflow distribution and temperature control during the curing process.
An adaptable chamber isn’t just about flexibility—it’s also about efficiency. By modifying the chamber’s layout, users can create optimal conditions for each curing technique, whether it’s convection, infrared, or even a combination of both. This approach not only improves curing quality but also helps save energy, as the oven can adjust to the specific requirements of each job rather than running at maximum capacity all the time.
Smooth Switching Between Convection and Infrared for Optimal Results
Switching between convection and infrared heat is a vital function for hybrid powder coating ovens. In many of these ovens, operators can shift from one heat source to another without disrupting the curing process. This capability is particularly beneficial when working with hybrid powders or substrates that require varying temperatures or heat intensities throughout the cure cycle.
The transition between the two heat sources is typically managed by advanced controls that regulate how and when each type of heat is applied. The ability to switch heat sources efficiently helps maintain consistent results and reduces the risk of under- or over-curing. It also allows manufacturers to experiment with different curing profiles, which can be especially useful when working with custom coatings or unique materials.
Unified Control Systems for Managing Hybrid Heat Profiles
One of the most innovative features of modern powder coating ovens is the unified control system. This system simplifies the management of hybrid heat profiles by offering a centralized interface where operators can set and monitor temperature, airflow, and timing. Unified controls make it easier to maintain consistent heat distribution, whether using convection, infrared, or a combination of both.
These control systems are designed to be user-friendly, often featuring touchscreen interfaces or programmable settings that allow operators to customize curing profiles with ease. This precision is essential for achieving consistent results, particularly when dealing with complex coatings that require specific temperature ranges. By managing hybrid heat profiles from a single control point, manufacturers can ensure optimal curing results across different types of powder coatings.
Balanced Airflow Dynamics to Support Complex Curing Needs
Balanced airflow is critical for achieving uniform curing in powder coating ovens, especially when hybrid techniques are involved. Advanced ovens are equipped with dynamic airflow systems that ensure heat is distributed evenly throughout the chamber, regardless of the heat source being used. This balance prevents hot spots and ensures that every part of the coated surface receives the necessary heat for proper curing.
The role of airflow in hybrid curing is often underestimated, but it is a key factor in achieving high-quality finishes. By managing airflow dynamics, powder coating ovens can support complex curing requirements, whether for large batches or intricately shaped parts. Consistent airflow also helps maintain energy efficiency, as the oven can operate effectively without overheating specific areas.
Compatibility with UV-Assisted Curing for Specialized Coatings
Some advanced powder coating ovens are even compatible with UV-assisted curing techniques, opening new possibilities for specialized coatings. While not all powder coating processes require UV curing, it can be incredibly beneficial for certain finishes that need a quick surface cure or additional durability. Powder coating ovens equipped for UV curing have built-in systems that allow for easy integration of UV lamps alongside traditional heat sources.
This compatibility offers a wider range of curing options, making these ovens suitable for a broader variety of applications. The combination of heat and UV light can speed up the curing process while also enhancing the finish’s resistance to wear and tear. For manufacturers working with cutting-edge coatings, having the option to incorporate UV curing into their existing powder coating ovens adds another layer of versatility and performance.